A new McKinsey report underscores the importance of securing a steady supply of critical battery materials to support the global transition to net-zero, as demand for battery electric vehicles (BEVs) accelerates toward the end of the decade.
By 2030, annual BEV sales are expected to rise from 4.5 million units in 2021 to 28 million—a sixfold increase. McKinsey warns that this rapid growth could lead to “persistent long-term challenges” in meeting material demand.
The report also highlights growing efforts by automakers to reduce Scope 3 emissions linked to material sourcing, making sustainable battery production increasingly vital. However, McKinsey’s projections indicate that demand for key raw materials may exceed baseline supply, potentially causing shortages, price fluctuations, and the need for substantial new investment.
Supply shortages looming
According to McKinsey’s report, battery manufacturers are likely to face significant challenges in securing adequate supplies of essential raw materials by 2030, based on current market trends.
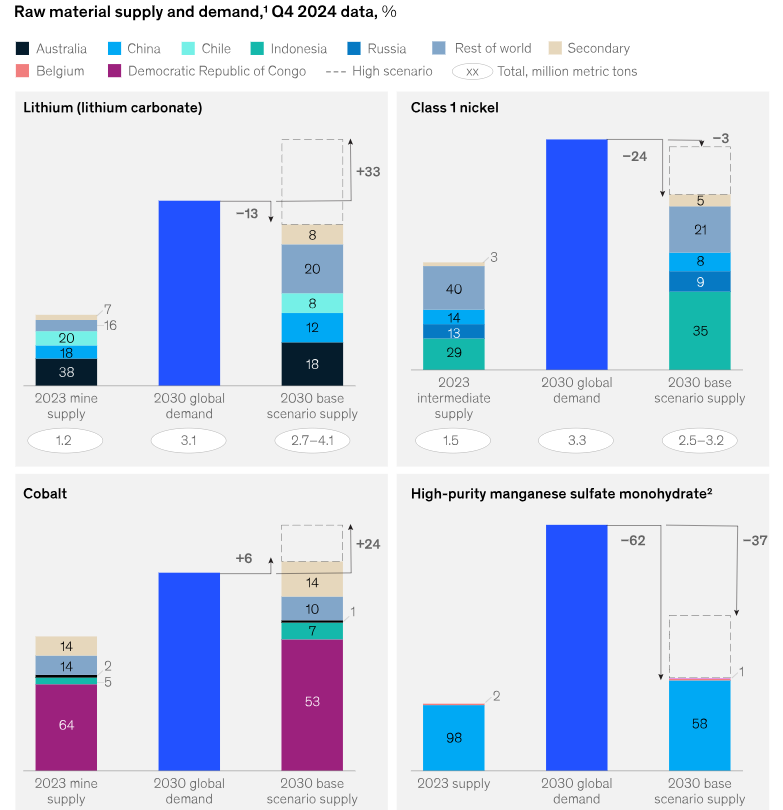
McKinsey’s report highlights that over 80% of mined lithium currently goes to battery production—a figure projected to rise to 95% by 2030. With technological shifts favoring lithium-heavy batteries, lithium mining will need a significant boost to meet surging demand.
Nickel:
Concerns over shortages due to BEV expansion have driven large investments in new mines, especially in Southeast Asia. However, McKinsey warns that even with increased output, competition from the steel industry for Class 1 nickel could lead to a slight shortfall by 2030.
Cobalt:
Although battery chemistries are expected to use less cobalt, overall demand could still grow by 7.5% annually through 2030. McKinsey notes that cobalt shortages are unlikely but emphasizes that its supply is closely tied to nickel and copper production, as it is mainly a byproduct.
Manganese:
While manganese supply is set to increase, the availability of battery-grade HPMSM (high-purity manganese sulfate monohydrate) may remain constrained. McKinsey’s base-case scenario suggests only 20% of HPMSM production will meet battery-grade standards, increasing to 30% if all announced refinery projects come to fruition. However, demand for HPMSM will account for just 5% of total manganese demand.
LFP (Lithium Iron Phosphate) Adoption Scenarios:
McKinsey also models the impact of accelerated LFP battery adoption. In a scenario where LFP use rises but EV production growth slows, the demand dynamics for key battery materials like lithium, manganese, and nickel could shift significantly, potentially easing pressure on certain raw materials.
The report underscores that strategic investments in refining and production capacity will be essential to balancing supply and demand in the coming decade.
Although demand for batteries and raw materials is surging, McKinsey highlights that supply remains heavily concentrated in resource-rich nations—nickel from Indonesia, lithium from Argentina, Bolivia, and Chile, and cobalt from the Democratic Republic of Congo (DRC).
Refining Concentration:
Refining operations for key materials also remain geographically clustered, with China dominating cobalt and lithium refining, Indonesia focusing on nickel, and Brazil refining niobium.
This supply chain structure poses strategic challenges for regions like the EU and US, which heavily depend on imports. For example, the EU sources 68% of its cobalt from the DRC, 24% of its nickel from Canada, and 79% of its refined lithium from Chile.
Transparency and ESG Concerns:
Supply chain transparency for materials such as refined nickel, cobalt, and lithium is often incomplete. China produces over 95% of high-purity manganese and refines nearly all graphite used in battery anodes. This limited visibility raises ESG concerns, prompting initiatives like the EU Batteries Regulation, which aims to ensure sustainability from sourcing to recycling.
Supply Chain Resilience:
Recent disruptions in materials such as magnesium, silicon, and semiconductors (2021–2023) have heightened the need for resilient supply chains. Risks are further amplified by trade restrictions, such as China’s export controls on synthetic and natural graphite and Indonesia’s nickel ore export ban.
McKinsey emphasizes that as geopolitical tensions and regulatory pressures grow, improving transparency and diversifying supply sources will be crucial to meeting global battery demand sustainably.